Unlocking Efficiency: The Rise of the Connected Worker in Modern Industries
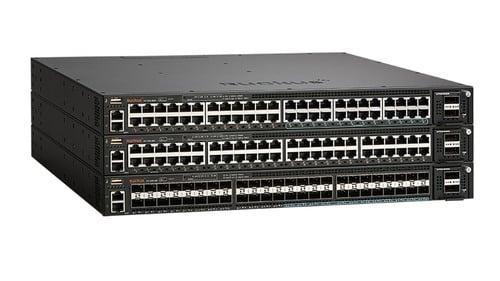
In today’s fast-paced world, the way we work is evolving at lightning speed. The concept of the connected worker has emerged as a game-changer across various industries. Imagine a workforce that seamlessly collaborates through technology, sharing real-time data and insights to drive productivity and innovation. This isn't just a dream—it's happening now.
With tools like mobile devices, IoT gadgets, and cloud-based software becoming staples in workplaces everywhere, companies are starting to realize the tremendous benefits of having a Connecting workers. From improved communication to enhanced efficiency, the advantages are clear. As organizations embrace this shift towards connectivity, they unlock new opportunities for growth and success.
Join us as we explore what it means to be a connected worker in modern industries. We will dive into compelling case studies showcasing businesses that have harnessed this strategy effectively while also peering into future predictions about its role in shaping tomorrow's workplace dynamics. Get ready to discover how connectivity is transforming not only individual roles but entire organizations!
The benefits of having a connected workforce
A connected workforce enhances communication across all levels of an organization. Team members can easily share insights, ask questions, and collaborate in real time, regardless of their physical location. This fluid exchange fosters a culture of openness and encourages innovative thinking.
Another significant advantage is increased productivity. With access to digital tools and resources, employees can streamline their workflows. They spend less time searching for information or waiting on approvals.
Moreover, connected workers benefit from better data access. Real-time analytics empower them to make informed decisions quickly. This agility allows businesses to respond faster to market changes and customer needs.
Additionally, employee engagement sees a boost when teams feel interconnected. A sense of belonging drives motivation and job satisfaction—key components for retaining top talent in competitive industries.
Case studies of companies implementing connected worker strategies
Siemens is a prime example of leveraging connected workers. The company integrated IoT devices into its manufacturing processes. This initiative allowed real-time monitoring and data collection, leading to increased efficiency.
Another notable case is Honeywell. They introduced wearables that provide employees with critical information on demand. These tools significantly reduce downtime while enhancing safety standards across operations.
Then there's Bosch, which implemented augmented reality training for technicians. By using AR glasses, they can access manuals and receive step-by-step guidance during repairs or installations. Productivity soared as complex tasks became more manageable.
GE adopted digital twin technology in various plants. It creates virtual models of physical assets, enabling teams to predict maintenance needs effectively and minimize operational disruptions.
These companies showcase the transformative power of connected worker strategies across industries today.
Future predictions for the role of connected workers in industries
The landscape of work is evolving rapidly, and the role of connected workers is set to expand even further. As technology continues to advance, industries will see increased integration of AI, IoT devices, and cloud solutions into daily operations. This shift will create an environment where connected workers can thrive.
Future workplaces may leverage augmented reality for training purposes or remote support. Imagine technicians receiving real-time guidance through AR glasses while performing complex tasks on-site. This capability could drastically reduce error rates and improve efficiency.
Moreover, as data analytics become more sophisticated, companies will harness insights from connected worker platforms to optimize workflow processes continually. Predictive maintenance in manufacturing is one area that stands to benefit immensely; machines equipped with sensors can alert teams before issues arise, minimizing downtime.
As remote working solidifies its place in various sectors, the concept of the connected worker will also evolve beyond traditional office environments. Remote collaboration tools will ensure that team members stay engaged no matter their location.
For more info. Visit us:
- Questions and Answers
- Opinion
- Story/Motivational/Inspiring
- Technology
- Art
- Causes
- Crafts
- Dance
- Drinks
- Film/Movie
- Fitness
- Food
- Παιχνίδια
- Gardening
- Health
- Κεντρική Σελίδα
- Literature
- Music
- Networking
- άλλο
- Party
- Religion
- Shopping
- Sports
- Theater
- Wellness
- News
- Culture
- War machines and policy