What is a 72-hour Salt Spray Test and 48-hour Salt Spray Test?
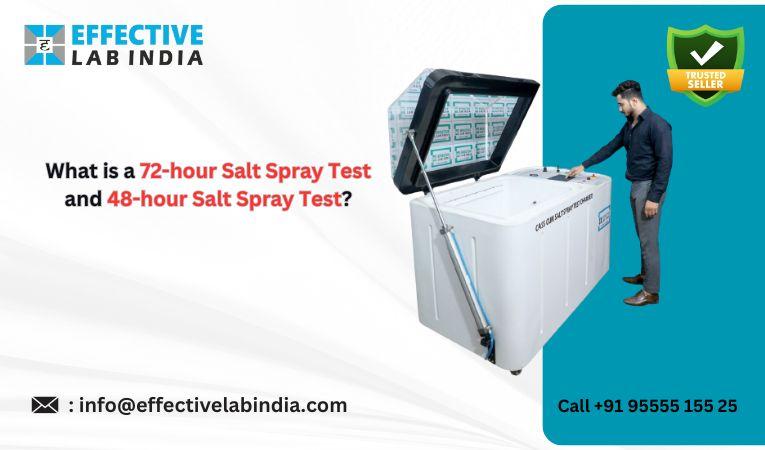
The salt spray test is one of the most popular ways to evaluate corrosion resistance in the field of material testing, particularly for metals and coatings. In the industrial industry, corrosion is a big problem that affects everything from consumer electronics to car parts. It's imperative for everyone involved in product development, quality assurance, or industry standard compliance to comprehend the 48- and 72-hour salt spray tests.
Understanding Salt Spray Testing
A standardised salt spray test procedure used to assess the corrosion resistance of materials and coatings is salt spray testing, sometimes referred to as salt fog testing. It is especially common in fields where exposure to hostile environments is frequent, such construction, automotive, and aerospace. Through the simulation of prolonged exposure to seawater, this test aids manufacturers in forecasting the durability of their products in corrosive conditions.
How Does the Salt Spray Test Work?
A sample material is put in a salt spray chamber and subjected to a fine mist of saltwater solution—typically sodium chloride (NaCl)—continuously during the salt spray test. The chamber's environment is controlled, with a constant temperature of approximately 35°C (95°F) and a relative humidity of 95–100%. The material's interaction with the salt mist accelerates the process of corrosion over time. Although the test's duration might vary, 48 and 72 hours are among the most typical times.
What is the 72-Hour Salt Spray Test?
The purpose of the 72-hour salt spray test is to expose materials to the corrosive environment of the salt spray test chamber for a longer period of time. over materials that are anticipated to withstand harsh circumstances over extended periods of time, this test is especially helpful. The material is tested for three full days in the chamber, allowing for a more thorough evaluation of its corrosion resistance.
Application and Relevance of the 72-Hour Test
This extended test is often used for products that have been built for use in harsh environments, such as outdoor building materials, marine supplies, and some vehicle parts. The 72-hour period allows for a more comprehensive understanding of the material's long-term performance, providing manufacturers with important information to ensure dependability and durability over the long run.
What is the 48-Hour Salt Spray Test?
Despite being shorter than the 72-hour version, the 48-hour salt spray test nevertheless yields a lot of information about a material's resistance to corrosive conditions. This time frame is frequently selected for materials that are not expected to be subjected to harsh environments or for initial testing stages.
Application and Relevance of the 48-Hour Test
The 48-hour salt spray test is used by consumer electronics, general building materials, and some automotive component industries. When rapid turnaround times are required for product manufacturing cycles or when the product is not anticipated to be exposed to corrosive environments for an extended period of time, this test is very pertinent.
Comparing 72-Hour and 48-Hour Salt Spray Tests
The duration is the main distinction between the 48- and 72-hour salt spray tests. The 72-hour test delivers a more thorough assessment, even though the 48-hour test offers insightful information on corrosion resistance. Extended exposure times facilitate the development of more substantial corrosion, which can uncover possible vulnerabilities that could not be seen in a shorter test.
Choosing the Right Test for Your Needs
Take into account the product's intended usage, environmental exposure, and industry norms while choosing between the 72- and 48-hour tests. The 72-hour test offers a higher level of assurance and is frequently more appropriate for products exposed to harsh circumstances. However, the 48-hour test may be enough for products with mild exposure or when testing time is limited.
Importance of Salt Spray Testing in Quality Control
Ensuring Product Durability and Longevity
To ensure that products can survive corrosive environments and increase their durability and lifetime, salt spray testing is essential. This is especially crucial in sectors of the economy where serious safety risks or monetary losses can result from corrosion-related product failure.
Meeting Industry Standards and Regulations
Salt spray testing is required by several industries' stringent standards to confirm corrosion resistance. It is usual practice to refer to standards like ISO 9227 and ASTM B117, which offer instructions on how to conduct tests and interpret the results. Respecting these guidelines is necessary for both market acceptance and regulatory compliance.
Conclusion
In conclusion, the 48- and 72-hour salt spray tests are very useful methods for determining how resistant materials and coatings are to corrosion. By using these tests, producers can make sure their products are durable, meet industry standards, and eventually reach consumers with dependable goods. Making decisions that are in line with industry standards and product needs is made possible by having a thorough understanding of the distinctions between the two tests and their respective uses.
FAQs
Q 1: How accurate is salt spray testing at forecasting corrosion in the actual world?
Although corrosion resistance can be reliably assessed using salt spray testing, this method should be considered an expedited test rather than a precise forecast of performance in real-world scenarios.
Q 2: Can tests using salt spray be kept longer than 72 hours?
Indeed, contingent upon the substance and the particular conditions of the examination, salt spray examinations may be prolonged past 72 hours.
Q 3: Which sectors gain the most from testing for salt spray?
Because these sectors require materials that are resistant to corrosion, salt spray testing is very beneficial to the automobile, aerospace, marine, and construction industries.
Q 4: What is the difference between other corrosion tests and salt spray testing?
Testing with salt spray is merely one way to evaluate corrosion resistance. diverse tests, like cyclic corrosion testing, could provide diverse perspectives on how a material performs under various circumstances.
Q 5: Do 48- and 72-hour salt spray tests cost significantly different amounts?
Longer tests are usually more expensive; the cost difference is usually proportional to the test's duration and specific criteria. The expense must be evaluated against the possible advantages of having more complete data, though.
- Questions and Answers
- Opinion
- Story/Motivational/Inspiring
- Technology
- Art
- Causes
- Crafts
- Dance
- Drinks
- Film/Movie
- Fitness
- Food
- Giochi
- Gardening
- Health
- Home
- Literature
- Music
- Networking
- Altre informazioni
- Party
- Religion
- Shopping
- Sports
- Theater
- Wellness
- News
- Culture
- War machines and policy