A Guide to the Process of PP Sheets: From Raw Material to Finished Product
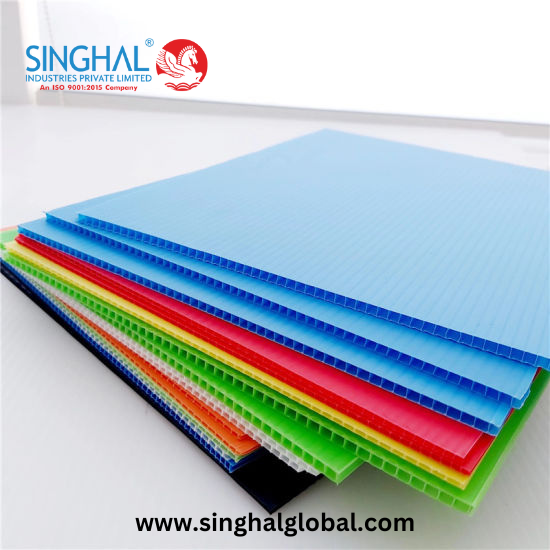
Polypropylene (PP) sheets have become a cornerstone in various industries due to their versatility, durability, and cost-effectiveness. Used in everything from packaging to construction, PP sheet price are a preferred choice for many applications. Understanding the manufacturing process behind these sheets provides valuable insights into their quality and performance. This guide walks you through the journey of PP sheets from raw material to finished product.
What Are PP Sheets?
PP sheets are thin, flat pieces of polypropylene, a type of plastic known for its robustness and flexibility. Polypropylene is a polymer derived from propylene monomers, which are chemical PP sheet for cable drum obtained from petroleum. PP sheets are widely used due to their resistance to chemicals, moisture, and high temperatures, making them ideal for various industrial and commercial applications.
The Manufacturing Process
The production of PP sheets involves several key stages, each critical to ensuring the final product meets industry standards. Here’s a step-by-step guide to how PP sheets are manufactured:
1. Raw Material Preparation
The journey begins with the preparation of polypropylene resin, the primary raw material for PP sheets. This resin is created through the polymerization of propylene gas. The polymerization process involves converting propylene gas into a solid polymer through a chemical reaction, usually using a catalyst.
-
Propylene Extraction: Propylene is extracted from crude oil or natural gas. This extraction process involves separating propylene from other hydrocarbons through distillation and other chemical processes.
-
Polymerization: Propylene is then polymerized in a reactor, where it undergoes a chemical reaction to form polypropylene resin. This resin is a white powder or small pellets that will later be used to produce PP sheets.
2. Compounding
Once the polypropylene resin is prepared, it needs to be compounded. This stage involves mixing the resin with additives to enhance its properties. These additives can include:
-
Colorants: To produce PP sheets in various colors.
-
Stabilizers: To improve the sheet’s resistance to UV light and heat.
-
Antioxidants: To prevent degradation of the resin during processing and throughout its lifespan.
The compounding process is conducted using an extruder, which heats and mixes the resin and additives to ensure a uniform blend.
3. Extrusion
Extrusion is a crucial step in the manufacturing of PP sheets. During extrusion, the compounded polypropylene is melted and formed into sheets. This process involves:
-
Melting: The compounded polypropylene is fed into an extruder, where it is heated to a high temperature until it melts into a viscous liquid.
-
Forming: The molten polypropylene is then forced through a flat die, creating a continuous sheet. The thickness of the sheet can be adjusted by changing the die settings.
-
Cooling: The extruded sheet is cooled rapidly using air or water to solidify it. This cooling process helps in achieving the desired thickness and surface finish.
4. Calendering
For some applications, the PP sheet may undergo a calendering process. Calendering involves passing the sheet through a series of rollers to achieve a specific thickness and surface finish. This process is particularly useful for producing thinner sheets with a smooth, even surface.
-
Rolling: The PP sheet is fed between rollers, which apply pressure and heat to reduce its thickness and improve its smoothness.
-
Cooling and Cutting: After calendering, the sheet is cooled and cut into the desired sizes and shapes.
5. Slitting and Cutting
Once the PP sheet has been extruded and, if necessary, calendered, it is cut into manageable sizes for various applications. This stage involves:
-
Slitting: For large rolls of PP sheet, the material is slit into narrower rolls or sheets, depending on customer specifications.
-
Cutting: Sheets are then cut into specific dimensions required for different uses. This cutting can be done using various methods, including guillotine cutters or laser cutting for precision.
6. Quality Control
Quality control is an essential part of the manufacturing process to ensure that the PP sheets meet industry standards and customer requirements. Quality checks typically include:
-
Thickness Measurement: Ensuring the sheet thickness is within specified tolerances.
-
Surface Inspection: Checking for any defects or irregularities on the surface.
-
Physical Testing: Testing properties such as tensile strength, impact resistance, and flexibility.
Quality control is conducted throughout the manufacturing process to identify and rectify any issues before the final product is shipped.
7. Packaging and Distribution
After passing quality control, the PP sheets are packaged and prepared for distribution. The packaging process involves:
-
Wrapping: Sheets are wrapped to protect them from damage during transportation and handling.
-
Labeling: Packages are labeled with relevant information, including product specifications and handling instructions.
-
Shipping: The packaged PP sheets are then shipped to customers or distributors.
Applications of PP Sheets
PP sheets are highly versatile and find applications across various industries, including:
-
Packaging: Used for containers, boxes, and protective covers.
-
Construction: Employed in building materials, insulation, and waterproofing.
-
Automotive: Used in vehicle interiors and components.
-
Medical: Utilized in medical packaging and laboratory equipment.
Conclusion
The manufacturing process of PP sheets is a complex journey from raw materials to finished products, involving careful preparation, compounding, extrusion, and quality control. Each stage is crucial to ensuring that the final product meets the high standards required for its diverse Polypropylene sheets manufacturers. As industries continue to demand more durable, versatile, and cost-effective solutions, PP sheets remain a popular choice, demonstrating their enduring value in the world of manufacturing and beyond.
Frequently Asked Questions (FAQs):
1. How does Singhal Industries ensure the quality of PP sheets throughout the manufacturing process?
Singhal Industries maintains high-quality standards by implementing rigorous quality control measures at every stage of the PP sheet manufacturing process. From the initial preparation of polypropylene resin to the final packaging, the company conducts thorough inspections and tests. This includes checking the thickness, surface finish, and physical properties of the sheets to ensure they meet industry standards and customer specifications. Quality checks are integrated throughout the process to address any issues promptly and maintain product consistency.
2. What makes Singhal Industries' PP sheets stand out in the market?
Singhal Industries' PP sheets are distinguished by their superior quality and performance, which result from the company's commitment to advanced manufacturing techniques and stringent quality control. The company uses state-of-the-art extrusion and calendering technologies to produce sheets with precise thickness and a smooth surface finish. Additionally, Singhal Industries offers customization options to meet specific customer needs, including various colors, thicknesses, and sizes. Their focus on using high-grade raw materials and incorporating innovative additives ensures that their PP sheets are durable, versatile, and reliable for a wide range of applications.
3. Can Singhal Industries customize PP sheets for specific industrial applications?
Yes, Singhal Industries offers customization options for PP sheets to cater to specific industrial requirements. The company provides tailored solutions, including adjustments in thickness, color, and surface finish, to meet the unique needs of different industries. Whether for packaging, construction, or other applications, Singhal Industries works closely with clients to understand their specifications and deliver PP sheets that align with their operational needs. This flexibility ensures that customers receive products that are not only high-quality but also precisely suited to their intended uses.
- Questions and Answers
- Opinion
- Story/Motivational/Inspiring
- Technology
- Art
- Causes
- Crafts
- Dance
- Drinks
- Film/Movie
- Fitness
- Food
- Giochi
- Gardening
- Health
- Home
- Literature
- Music
- Networking
- Altre informazioni
- Party
- Religion
- Shopping
- Sports
- Theater
- Wellness
- News
- Culture
- War machines and policy